Please click here to access the main AHDB website and other sectors.
Lean: driving waste out of business
Tuesday, 18 December 2018
Grace Emeny answers your questions about lean and why horticultural businesses might benefit from introducing it into their business
The concept of Lean has been around for decades; why is it so important now?
Lean is probably more widely recognised in factories these days, having famously taken hold at Japanese car manufacturer Toyota in the 1980s.
However, today, with Brexit and uncertainties around access and availability of labour, we need to demonstrate thought leadership and to equip growers with the tools to make labour more efficient and drive out waste and non-added value elements of our businesses.
What are the key tenets of Lean?
There are six basic principles of Lean:
- Focus on the customer
- Understanding and identifying how work gets done
- Manage, improve and smooth out the process flow
- Identify the non-added value elements and waste
- Manage by using fact and data, and reduce variances
- Attain continuous improvement
What are the easiest and most common changes businesses can make to start applying Lean principles?
As a useful starting point for businesses you need to identify suitable staff through the whole end-to-end chain. These newly empowered staff members will be your Lean champions. Those staff will already be aware of potential savings, efficiencies and what best practice looks like, but may not have had the vehicle or perceived route to engage. Attention to detail, applying small differences soon adds up to some significant savings and efficiencies.
Can Lean apply to all businesses or just certain types?
All businesses of any size or type can apply the principles of Lean. We might think of the packhouse as the obvious place which might give some quick wins but operations in the crop can also benefit. For example, with harvesting being a more difficult nut to crack for automation it makes a lot of sense to look at this part of the business as well.
What’s been the biggest success you’ve seen with Lean?
The biggest success I’ve seen was with a speciality tomato grower who identified a waste stream. They applied a very simple solution that saved them around £65,000 a year. The real success story for this company was that they have now gone through the same Lean process with different parts of the business to continue to save and make efficiencies throughout the whole supply chain.
How is AHDB helping to promote this way of thinking?
We’ve previously commissioned work around both Lean and the champion worker initiatives. We ran a study of six diverse growers and identified the gains to be had by businesses of all shapes and sizes.
Using the information from these studies, along with the collective experience of four consultants with Lean and labour efficiency expertise, we ran a series of workshops to help businesses either to get started with the process or add to the progress they have already made. Due to the success of these events, a new series of labour efficiency workshops will run early in 2019.
The workshops and study identified a real need to improve the skills training for supervisors, something that was common to all horticultural sectors. The first wave of ‘Supervisor Skills Workshops’ run until March 2019. To book your place, click here.
The labour efficiency workshops are being run as part of AHDB’s SmartHort campaign, designed to help improve labour productivity in horticulture. To find out more, visit visit ahdb.org.uk/smarthort.
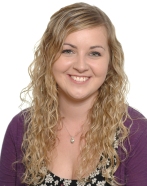
Topics:
Sectors:
Tags: